„Amerykański przemysł samochodowy jest w kryzysie”.
To złowieszcze zdanie otwiera 220-to stronnicowy raport opublikowany w 1982 roku przez National Accademy Press. Nie „przechodzi chwilowe trudności”, „ma wyzwania” czy „boryka się z problemami”. Jest w kryzysie. Przez ostatnie dekady amerykańskie firmy samochodowe nieustannie traciły udział w swoim rynku od praktycznego monopolu w 1955 roku do 75% w roku 1980.
Konkurencja z Japonii
Chociaż za część importu odpowiedzialni byli europejscy producenci to największe zagrożenie dla amerykańskiego przemysłu stanowiły firmy japońskie. Były w stanie dostarczyć znacząco tańsze samochody, jednocześnie zapewniając wyraźnie wyższą jakość. Amerykanie zarzucili Japończykom stosowanie cen dumpingowych, przypisywali ich sukces taniej sile roboczej, wyzyskowi pracowników, aż po teorię spiskową koordynacji wszystkich firm przez rząd (Japan, Inc). Dopiero kiedy odrzucono wszystkie te tezy Amerykanie zrozumieli, że przewaga Japończyków wywodzi się z innego systemu pracy.
Masowa Produkcja
Zanim jednak przyglądniemy się systemom produkcji japońskich firm, warto zrozumieć w jaki sposób działała większość firm motoryzacyjnych w latach 80-tych XX-go wieku. Bazowały one na koncepcji Masowej Produkcji opracowanej przez Henrego Forda na początku wieku i rozwiniętej przez Alfreda Sloana w General Motors. Idea była prosta – produkcja na masową skalę zmniejsza cenę jednostkową produktu. Czyli im więcej produkujesz, tym niższą cenę możesz osiągnąć. Obniżona cena miała jednak sporo konsekwencji. Firmy dążyły do pełnej utylizacji zasobów. Dlatego maszyny nie mogły stać bezczynne, a linia produkcyjna zostać zatrzymana, za wyjątkiem sytuacji zagrażających życiu lub zdrowiu. Przezbrojenie maszyny (przestawienia jej na produkcję innych części) lub linii (produkcja innego typu samochodów) było źle widziane, bo maszyna wtedy nie pracowała. Tym samym, żeby ograniczyć przestoje i przezbrojenia, produkowano w dużych partiach, tworząc olbrzymie zapasy, nawet jeżeli w danym momencie nie było na nie zapotrzebowania.
System Produkcyjny Toyoty
Tymczasem Japońskie firmy (a w szczególności Toyota) stosowały wręcz odwrotne podejście. Części były produkowane tylko, gdy było na nie zapotrzebowanie. Częste przestawianie maszyn było widziane jako korzyść. I każdy liniowy pracownik miał prawo pociągnąć za linkę sygnalizacyjną (Andon) i zatrzymać linię produkcyjną w przypadku zauważenia problemu. Innymi słowy Toyota odrzuciła kult utylizacji.
Mimo to TPS (Toyota Production System) działał bardzo dobrze. Co więcej, można było zobaczyć gigantyczne różnice między fabrykami amerykańskimi i japońskimi. Na przykład fabryka w USA miała zapasu chłodnic na 5 dni, natomiast ta w Japonii, zaledwie na 2 godziny. Tym samym Amerykanie mieli dużo więcej gotówki (584 USD) zamrożonej w częściach niż Japończycy (74 USD). Pozwalało to nie tylko zmniejszyć koszty, ale również zaoszczędzić przestrzeń i zwiększyć porządek i widoczność w fabryce.
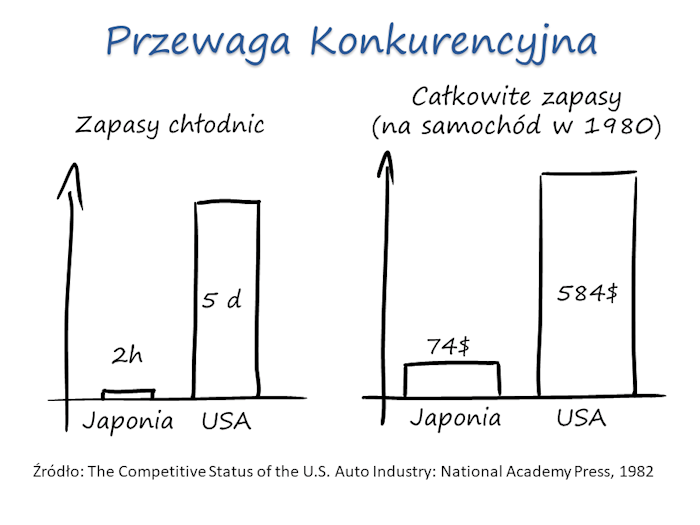
Różnica była tak rażąca, że pewien amerykański dyrektor odwiedzający fabrykę w Japonii w latach 80-tych stwierdził:
„Pokazali nam jakąś atrapę. Fabryka nie może istnieć bez zapasów.”
Porządek na linii produkcyjnej wpływa na ilość pracy potrzebnej do wykonania samochodu (112 godzin dla Forda i 47 dla Toyoty) i ilości defektów na samochód (3,7 dla Forda i 0,7 dla Toyoty – pamiętaj, to są lata 80-te).
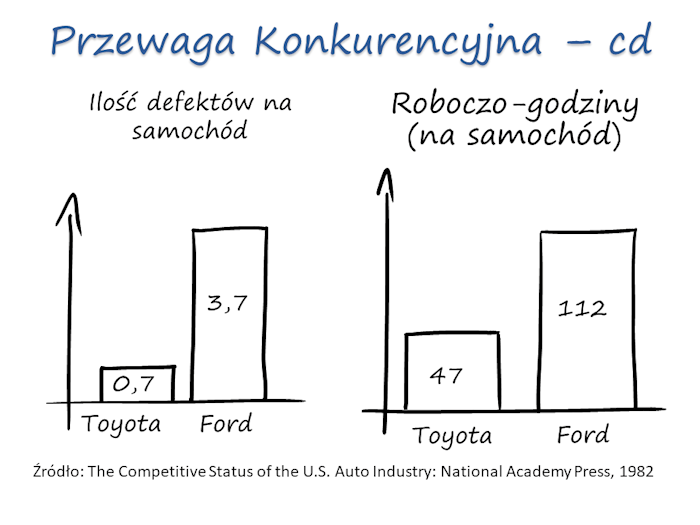
Toyota, dzięki rozwijanemu od lat 60-tych nowatorskiego podejścia przekształciła się z niewielkiej lokalnej firmy produkującej niskiej jakości pojazdy do największego producenta aut, wyprzedzając General Motors w 2008 roku (od tamtej pory koszulkę lidera straciła tylko raz w roku 2011 na rzecz Grupy Volkswagen).
Lean, czyli szczupła produkcja
Amerykanie ochrzcili System Produkcyjny Toyoty mianem Lean, czyli szczupłej produkcji. Przez następne dziesięciolecia namiętnie kopiowali jego elementy. Analizowali strumień wartości (Value Stream Mapping), poszukiwali straty, uruchamiali systemy Kanban i Andon. Mimo to dalecy byli od osiągnięcia sukcesu Toyoty. Zmiany były powierzchowne a wyniki często były widoczne jedynie na papierze. Tak jak wiele firm decydujących się na Agile, tak i firmy wybierające Lean często nie zauważały jednej istotnej rzeczy.
Kultura Lean
W 2001 roku Toyota spisała swoje wartości w „Drodze Toyoty”. Ten wewnętrzny dokument wyraźnie opisuje co jest najważniejsze w firmie. Nie są to narzędzia (jak Kanban) czy techniki (jak VSM czy identyfikacja strat). Są to natomiast dwa filary i pięć wartości na nich opartych, czyli:
Ciągłe Doskonalenie
poprzez Wyzwania, Kaizen (ciągła poprawa) i Genchi Genbutsu (poszukiwanie informacji u źródeł, czyli najczęściej na linii fabrycznej).
Szacunek dla Ludzi
poprzez Pracę Zespołową i Okazywanie Szacunku wszystkim pracownikom, klientom i dostawcom.
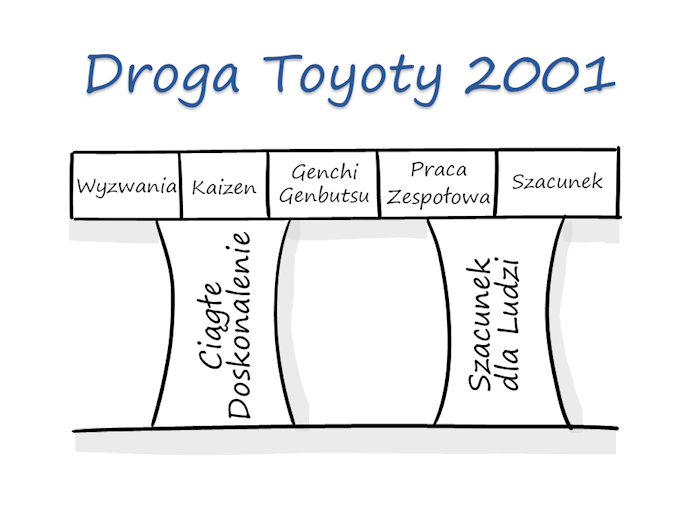
Tym samym Lean jest przede wszystkim kulturą nastawioną na ciągłe doskonalenie w oparciu o szacunek dla ludzi. Narzędzia, procesy i techniki są przydatne tak długo jak dostarczają wartość. Kiedy Toyota odkryje lepszy sposób sterowania produkcją niż Kanban to porzuci tą technikę. Tak jak w Agile, tak i w Lean zrozumienie „dlaczego” coś robimy jest ważniejsze od „co robimy”. Tak samo też kopiowanie zachowań nie przyniosi oczekiwanych rezultatów, a jedynie frustruje pracowników.
Lean Software Development
Na początku XXI wieku Mary Poppendieck przeniosła swoje doświadczenie z firm Lean do świata tworzenia oprogramowania. Przetłumaczyła zarówno koncepcje jak i pokazała w jaki sposób wykorzystać konkretne praktyki.
Książki i artykuły o Lean
Jeżeli chcesz poznać więcej szczegółów na temat Lean to zachęcam Cię do lektury:
- James P. Womack, Daniel T. Jones, Daniel Roos Machine that changed the world
- Jeffrey K. Liker Toyota Way (polskie wydanie „Droga Toyoty”)
- Książki Mary i Toma Poppendieck:
- Artykuły na naszym blogu
Zobacz również rozbudowaną listę książek Lean po polsku.